Additive and Advanced Ceramics Design Guide
SiC Opportunities
Refractory ceramics exhibit unique high-temperature properties that enable high-performance energy and propulsion systems. Silicon carbide is such a representative refractory ceramic, as no degradation in strength is observed up to at least 1500°C, and there is a clear advantage in strength and fracture toughness at high temperatures. Thermal creep is essentially absent in silicon carbide until temperatures in excess of 1400°C are reached. Oxidation rates in air and steam or combustion environments are exceptionally low until the protective silica layer that forms in those environments melts at >1700°C.
While simple geometries (e.g., plate and pipe) from refractory ceramics can be produced today, components of higher complexity (e.g., heat exchangers, flanges, turbines) may not be readily produced using current technologies. The ability to use refractory ceramics for these components will greatly improve the thermal efficiency of these energy systems well beyond what is possible with conventional metal systems. High-temperature Ni-based superalloys are currently limited to ~800°C.
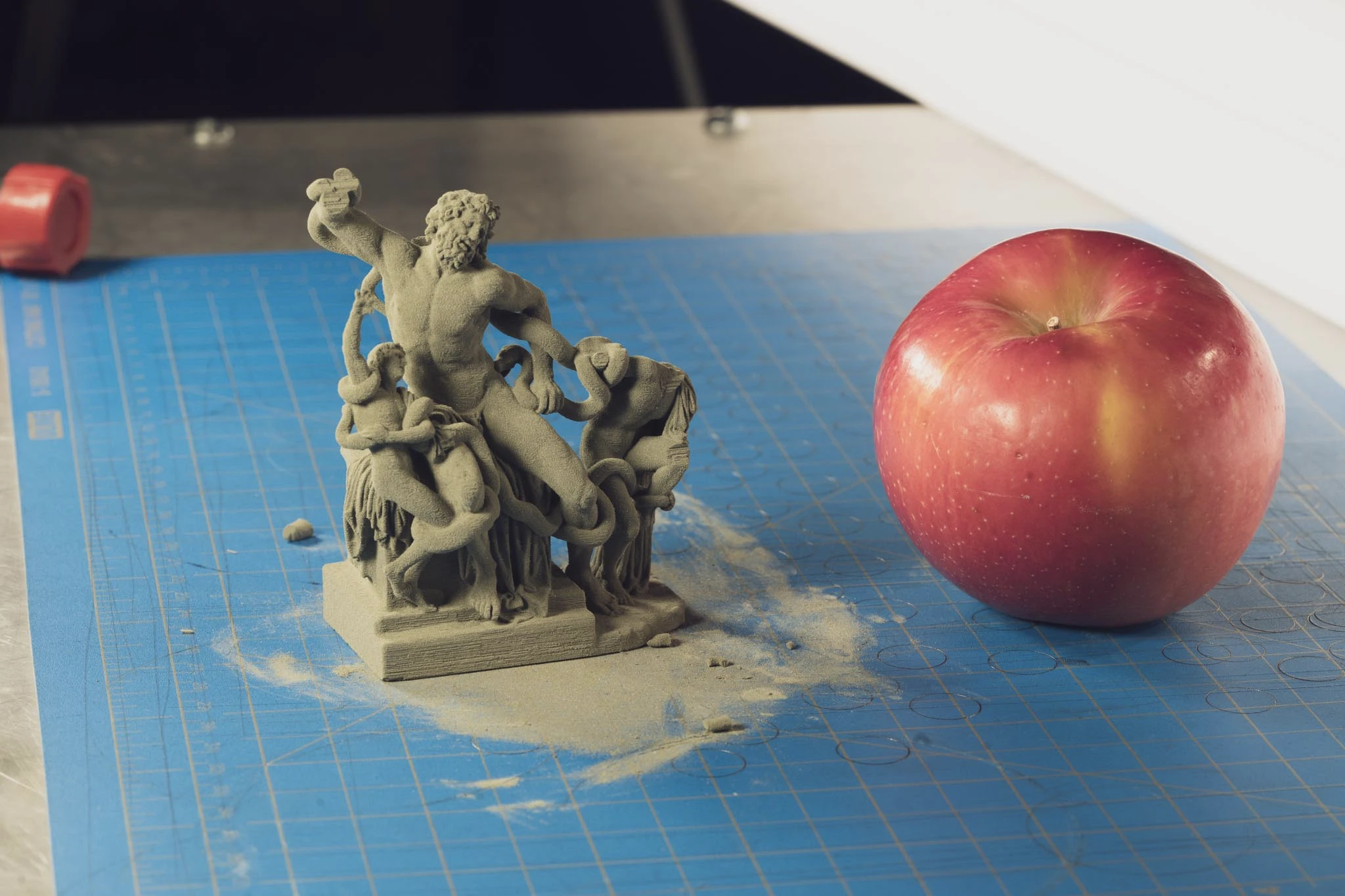
Material Properties
Thermophysical Properties
For simple design and scoping, we recommend the following thermophysical properties roughly at room temperature. Click on the material tab to see the properties for that material.
- SiC
- ZrC
- ZrO2
- B4C-SiC
- ZrHx
- YHx
Silicon Carbide
Property | Value | Unit |
---|---|---|
Maximum part size | 800×500×400 | mm |
Part tolerance | < 0.15 | mm |
Density | 2.6 - 3.2 | g/cc |
Coefficient of thermal expansion | 4.5 | ppm/K |
Thermal conductivity | 35 | W/m-k |
Strength | > 200 | MPa |
Zirconium Carbide
Property | Value | Unit |
---|---|---|
Maximum part size | 400×250×250 | mm |
Part tolerance | < 0.15 | mm |
Density | 5 - 6.7 | g/cc |
Coefficient of thermal expansion | 6.7 | ppm/K |
Thermal conductivity | > 15 | W/m-k |
Strength | > 150 | MPa |
Zirconium Oxide
Property | Value | Unit |
---|---|---|
Maximum part size | 400×250×250 | mm |
Part tolerance | < 0.2 | mm |
Density | ~3 | g/cc |
Coefficient of thermal expansion | 10 | ppm/K |
Thermal conductivity | < 0.5 | W/m-k |
Compressive Strength | > 10 | MPa |
Boron Carbide-Silicon Carbide
Property | Value | Unit |
---|---|---|
Maximum part size | 400×250×250 | mm |
Part tolerance | < 0.15 | mm |
Density | 1.2-1.7 | g/cc |
Coefficient of thermal expansion | ~ 4.5 | ppm/K |
Thermal conductivity | < 10 | W/mK |
Compressive Strength | > 200 | MPa |
Zirconium Hydride
Property | Value | Unit |
---|---|---|
Maximum part size | 250×50×50 | mm |
Part tolerance | < 0.1 | mm |
Density | 5.6 | g/cc |
Coefficient of thermal expansion | 20 | ppm/K |
Thermal conductivity | > 40 | W/m-k |
Strength | > 40 | MPa |
Yttrium Hydride
Property | Value | Unit |
---|---|---|
Maximum part size | 250×50×50 | mm |
Part tolerance | < 0.1 | mm |
Density | 4.25-4.3 | g/cc |
Coefficient of thermal expansion | 8-14 | ppm/K |
Thermal conductivity | 70 | W/m-k |
Strength | 80 | MPa |
For more detailed design and prediction, we recommend utilizing past reports on our methods.
Impurities
Our method does not introduce impurities to the feedstock. In fact, the process scrubs away almost all of the impurities present in the starting feedstock, except for a negligible increase in Cl and K impurities. It is clean enough to be used in nuclear fuels.
General Design Principles
Minimum Feature Size
We advise making the smallest feature size at least 1 mm.
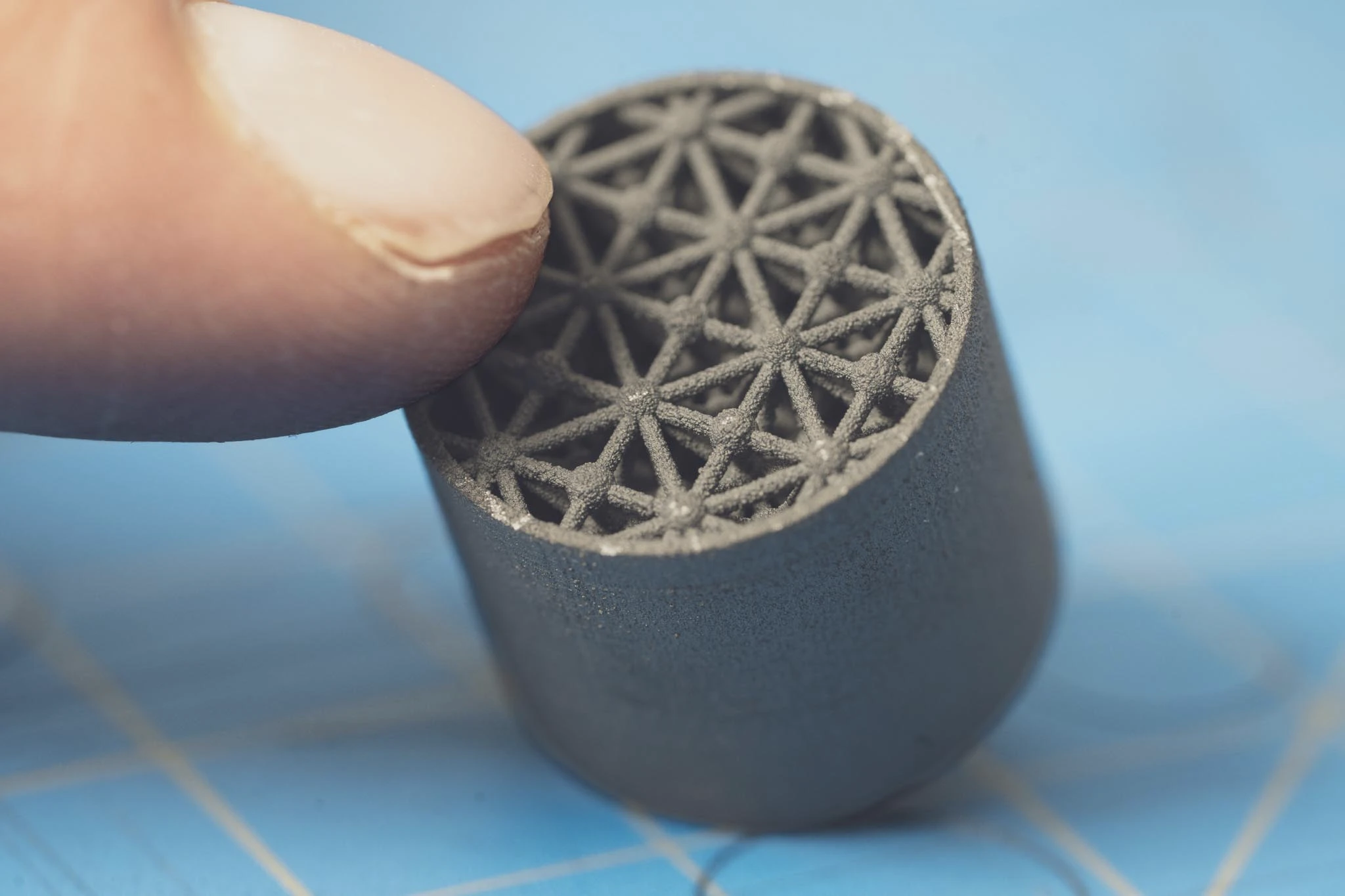
Minimum and Maximum Part Size
The printing beds have limited dimensions for different materials. See the above tables for details. Parts should fit inside the printing bed volume.
Larger parts can be produced by printing pieces and "welding" the pieces appropriately or by adding joining features.
Wall Thickness
- Walls should be between 1-20 mm thick.
- Thicker solid walls can be produced by creating walled cavities and embedding beads prior to the CVI process.
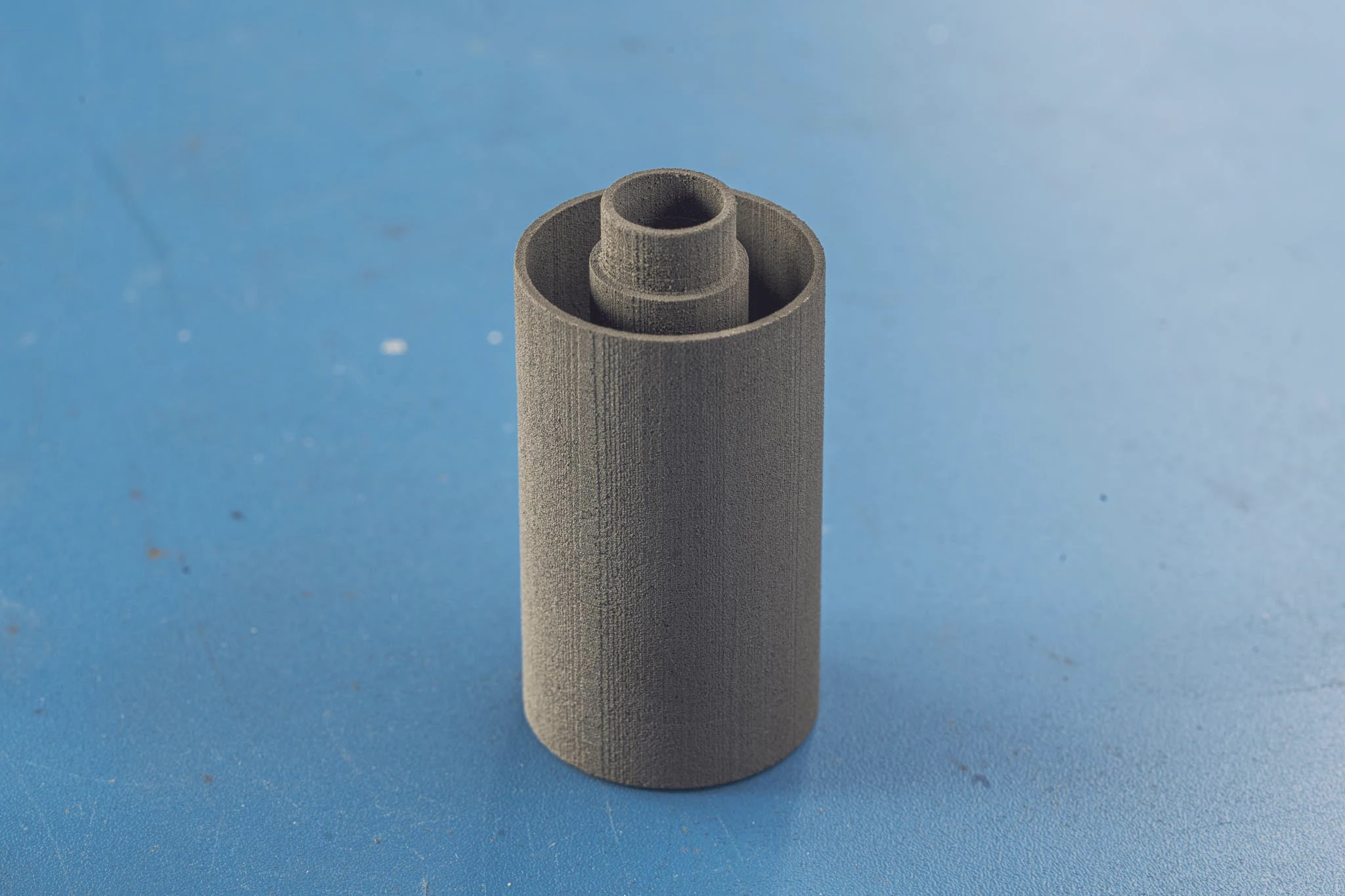
Markers and Indicators
2D design features can be added to the surface of parts by using a modeled inset. Examples include logos, QR codes, or serial numbers. This avoids using stickers or other identifying features that are not as thermally or chemically tolerant as SiC.
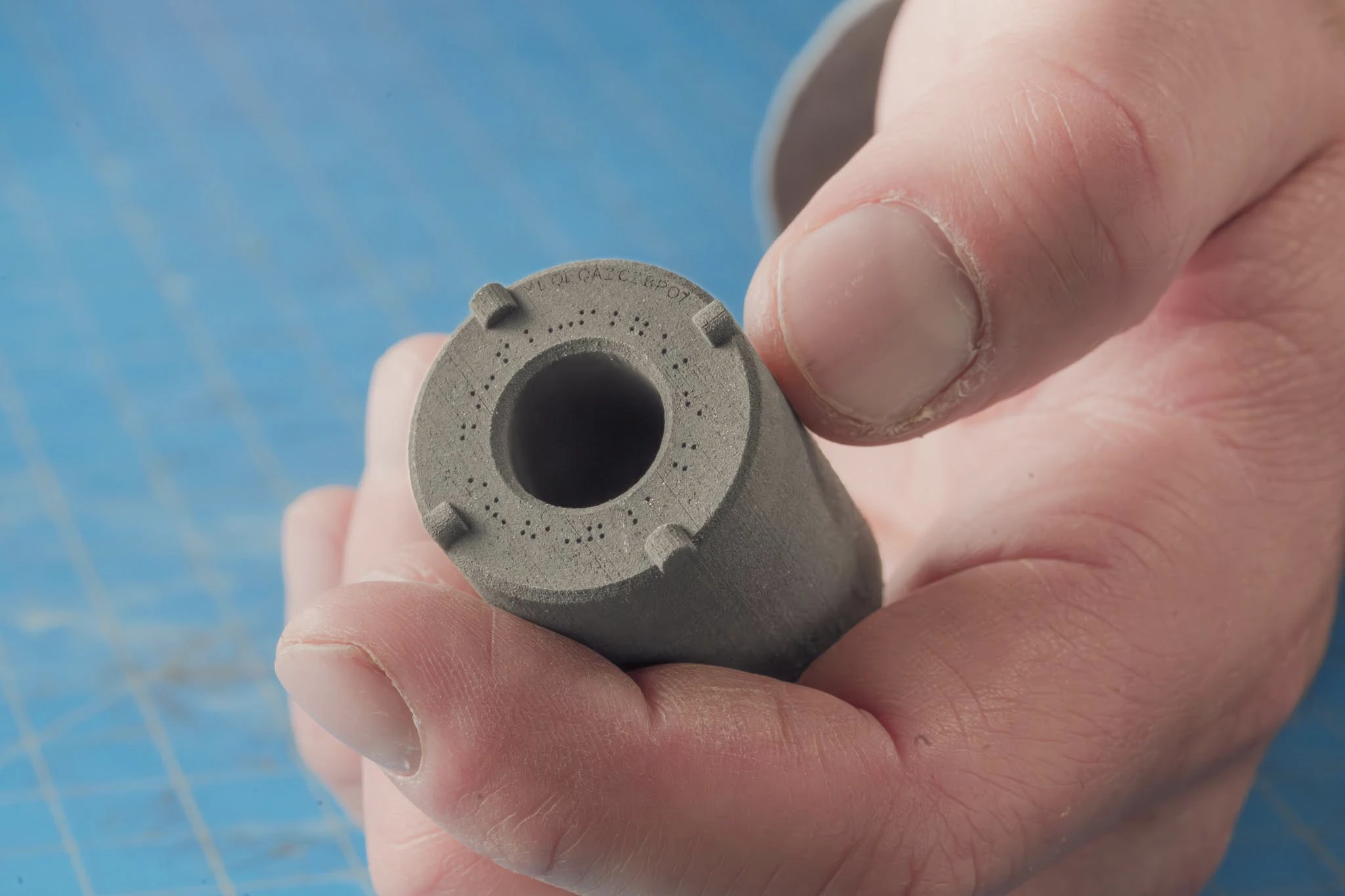
Cost Reduction
- Cost is very roughly proportional to volume. Make your parts light and hollow. Use ribbing instead of solid parts.
- Nesting lowers cost. If you need a lot of parts, it helps if they can fit snugly next to each other or inside each other.
- Complex designs cost more than simple designs.
File Preparation
We will work with you to get your design into print-ready form. We prefer STEP and SLDPRT file formats, but also accept other 3D formats such as an STL. 2D drawings may also be used to create a custom 3D file for your review.
Technology
Our technology was born out of the US Department of Energy’s materials development for harsh environments. We are the only technology available for 3D printing highly pure, fully crystalline, and stoichiometric silicon carbide.
The method offers a high degree of freedom in geometric complexity without compromising on material properties. The method combines binder jet printing and chemical vapor infiltration (CVI) in a process capable of yielding a high-purity, fully crystalline ceramic — attributes essential for ideal performance in high-temperature and corrosive applications or in the presence of displacement damage.
The foundational R&D is documented in a series of papers and reports:
- 3D printing of high-purity silicon carbide
- Characterization of radiation damage in 3D printed SiC
- Oxidation of 3D-printed SiC in air and steam environments
- Irradiation stability and thermomechanical properties of 3D-printed SiC
- Mechanical and Thermophysical Properties of 3D-Printed SiC
- Additive manufacturing of silicon carbide for nuclear applications